Motivation
Endotherme Hochtemperatursynthesen stellen die volumenstärksten Prozesse in der chemischen Industrie dar, die am Anfang fast jeder Wertschöpfungskette stehen. Als Anwendungsbeispiel wird hier die H2-Herstellung aus Methan durch Reformierung (Dampf- oder CO2) verwendet.
In großtechnische Anlagen ist die Maximaltemperatur durch die Verwendung metallischer Reaktorrohre limitiert, der Werkstoff weist Probleme mit katalytischer Aktivität und Standfestigkeit auf. Die Rohre werden von außen autogen auf eine maximale Temperatur von ~ 900°C erhitzt. Die zugeführte Energie kann nur teilweise für die chemische Reaktion genutzt werden, der überwiegende Teil fällt in Form heißer Rauchgase an. Im Projekt sollen daher neuartige, gasdichte, oxidkeramische Faserverbundrohre mit eingebetteter elektrischer Beheizung entwickelt und die Funktionsweise mit Wärmetausch in einer Demonstratoranlage gezeigt werden.
Zielsetzung
Im Projekt soll durch die Entwicklung oxidkeramischer Verbundstoffe und einem neuen Reaktorkonzept eine Technologie entwickelt werden, die die Energieeffizienz, den Primärkraftstoffverbrauch und den CO2-Ausstoss in endothermen Hochtemperaturprozessen durch die Möglichkeit der elektrischen Beheizung erheblich reduziert.
Diese eOCMC-Rohre übertreffen mit Betriebstemperaturen von 1200°C und >100W/m² Leistungsabgabe klassische Rohrreaktoren aus Stahl deutlich.
In Zukunft werden folgende Ansätze zur Effizienzsteigerung der Gassynthese weiterverfolgt:
- Erprobung der faserverstärkter Oxidkeramiken für hohe Prozesstemperaturen bis 1250°C.
- Weiterentwicklung des in das Bauteil integrierten elektrischen Schichtheizleiters für eine leistungsfähige und effiziente Direktbeheizung bei hohen Temperaturen.
- Das Auftragen von katalytisch aktiver Substanzen auf der Rohrinnenseite oder -außenseite
- Wärmetausch der ein- und ausströmenden Gasströme für eine bedeutende Reduktion des Primärkraftstoffverbrauchs (Cold-In-Cold-Out-Prinzip)
Publikationen
2025
- D. Kleschew, M. Sentko, U. NiekenElectrically Heated Multilayer Ceramic Composite Tubes for High‐Temperature Endothermic Reactions2025, Chemie Ingenieur Technik
Kontakt
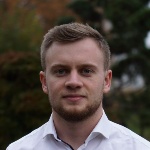
Daniel Kleschew
M.Sc.Wissenschaftlicher Mitarbeiter